品質管理と測定器の役割PDFダウンロード
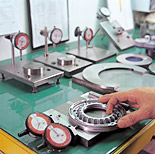
前回は「新規立上げ品の測定器準備」ということで、顧客から新規製品を受注した際に、受注決定から測定器の準備までに行うことを具体的に説明しました。
測定器を準備するまでの主な手順は下記の通りです。
- 工程毎の検査内容の決定
- 測定器の選定
- 測定器の設計
- 測定器の調達(手配・発注)
- ラインへの測定器の整備
自動車部品の品質管理
今回は、測定器の準備の前段階、自動車部品の品質管理について、そして、そもそも測定器が担う役割について説明します。自動車部品の製造において品質管理は極めて重要な要素です。自動車部品は高い品質基準を満たす必要があり、安全性、信頼性、耐久性などの面で確保されなければなりません。品質管理は、製品がこれらの基準を満たすことを確保するためのプロセスや手法の総称です。
製品や材料、サービスなどの規格や基準に従って、その品質や性能が要件を満たしているかどうかを評価することを「検査」と呼びます。検査は、品質管理や品質保証の一環として実施され、製品やサービスの信頼性や安全性を確保するために重要な役割を果たしています。その検査を行うために使用する道具が「測定器」あるいは「検査具」です。つまり、正確な測定結果に基づいて製品の品質を確保するために、測定器は品質管理プロセスの中で必要不可欠なツールなのです。
なお「検査」と「測定」の違いについて、下記記事において詳しく説明していますので参照ください。
測定器の担う役割
前述したように、自動車部品の品質管理においては、製品を検査し、規格に収まっていることを確認することが必要不可欠です。その製品検査に使うのが、「測定器」「検査具」です。
測定器が品質管理において担う主な役割は下記の通りです。
- 製品寸法の確認(検査)
測定器を使って自動車部品の製品仕様に基づいて測定および検査を行います。例えば、寸法、形状、角度、表面粗さなどを測定し、製品寸法が図面規格や製品仕様に合致しているかを確認します。製品の寸法が規格内であれば合格で「良品」、規格外であれば不合格で「不良品」と判定します。
なお、検査はどの工程で検査するかにより、「受入検査」、「工程内検査」および「出荷検査」に分類されます。 - 加工工程のモニタリング(工程管理)
製造プロセスの各段階で測定器を使用して測定を行い、加工工程のモニタリング(工程管理)を実施します。製品寸法を定期的に測定し、管理図などにプロットしてその推移をモニタリングすることによって、その製品寸法がどの程度変化しているかを確認します。
さらに、これらの測定データを解析することによって、加工工程の安定性や変動の傾向を把握し、必要に応じてプロセスの改善や修正を行います。具体的には、測定データを元に工程能力 Cp、Cpkなどを算出することによって工程の持つ能力を把握でき、工程の品質管理に役立ちます。 - 加工工程における製品の出来栄え寸法の調整
測定器を使って測定した製品寸法でその出来栄え寸法の調整に使用します。測定値が工程管理上狙った値から外れている場合、加工設備を調整して出来栄え寸法を修正します。なお修正した後は、再度出来栄え測定を実施し、狙った値になっていることを確認します。 - 品質記録の作成と追跡
測定器を使って測定した測定結果をチェックシート類に記録し、品質管理システムに追跡可能な形で保存します。この記録は製品の品質履歴のエビデンスとなり、必要な場合にはさかのぼりチェックなどに使用できます。 - 未然予防処置と品質改善支援
測定器での測定は、異常や欠陥を未然に検出する役割も果たします。
例えば、寸法の異常や不均一な特性を検出することで、製品の不良率を低減し、顧客への品質問題を未然に防ぐことができます。正確な測定データは、品質改善活動において品質の問題点を特定し、改善策を導くための貴重な情報源となります。測定データの解析や統計的手法を活用して、品質の問題点や改善のポイントを特定し、製品やプロセスの品質改善に貢献します。
* kensatoolsがお手伝いできること!!
上記のステップの中で、2)測定器の選定、3)測定器の設計、4)測定器の調達(手配・発注)にはかなりの時間が必要です。品質管理を担当者にとって、定常業務をこなしながらこれらのプラスの作業を行うことは時間的な余裕がなく、困難な場合が多いです(加工業の当社もそうなのでよく理解できます)。
そんな時には、kensatoolsがお手伝い致します。まずは相談してください。